Internal Rotary Inspection System (IRIS)
An advanced technique for accurate thickness measurement of tubes in air fin coolers, heat exchangers, boilers etc. Developed in late 50’s by Shell Oil for inspection of their Fin-Fan cooler tubes.
Now it is proven technique used world-wide for inspection and integrity assessment of Air fin coolers. Petroleum giants like Exxon-mobil, Shell, BP, KNPC, ADNOC, Flour-Daniel etc. are employing this technique regularly.
A computerized ultrasonic inspection system best suited for integrity assessment of air fin cooler tubes, which are inaccessible from external sides because of fins. It consists of a high frequency, highresolution transducer and 45 deg mirror mounted on a small water driven turbine. The mirror rotates at high speed and reflects the ultrasonic beam around the tube circumference to perform a 360 deg scan of the wall thickness.
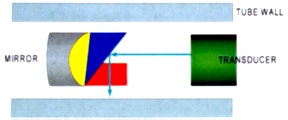
IRIS principle
Advantages
- High level of accuracy, as low as 0.05 mm size defect can be detected reliably.
- Only suitable and reliable NDT method for examination of finned tubes. Magnetic flux leakage and Eddy current testing are also used, primarily for initial sorting. However, these methods pose difficulty in
interpretation. - Unlike MFL or ECT, IRIS is suitable for ferrous as well as non-ferrous
and even non-metallic tubes. Test results are recordable in soft as well as hard formats. - The output display is user friendly. Accurate measurement even at support / baffle plate locations .
- The equipment is transportable and lightweight.
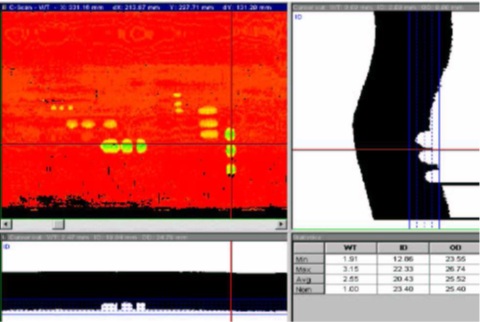
IRIS Result