Lixi Technique
Real time radiographic equipment for screening for corrosion in pipes. Main applications are CUI and corrosion under coatings in addition to locating blockage in process piping. The technique involves a Gadolinium-153 isotope
mounted on one side of a C-arm scanner and a detector on the opposite side.
Lixi, Inc. offers three products for this type of application: the Profiler, the Gadscope, and the Penetrator.
Lixi Profiler
The radiation beam is directed through the centre of the pipe measuring the double wall thickness. Data is presented in the form of a graph. The graph is produced instantly (in real time) and presented electronically on a computer (rather than on film). The scanner is moved along the length of pipe and each line scan measures the double wall thickness for a discreet section. For horizontal pipe the normal procedure is to perform 3 line scans measuring sections at 12 o’clock (0º)/6o’clock (180º), 45º /225º, 135º /315º (although this will depend on the pipe process and where corrosion is expected).
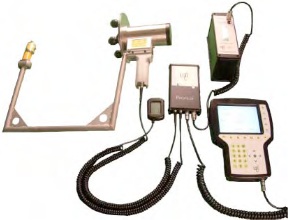
The Lixi Profiler
Lixi Gadscope & The Lixi Penetrator
The Lixi Gadscope uses a radioisotope of Gd-153 as the radiation source. The Lixi Penetrator uses an x-ray tube as the radiation source. In either system, the radiation beam is aimed tangentially so that it can real-time image the outer surface profile of the pipe at a given location (normally the 6 o’clock position on horizontal pipes) as well as features within the insulation. The Gadscope would be more appropriate than the Profiler for larger diameter pipework containing dense product. It provides a qualitative result but could be used to complement the more quantitative Profiler when it’s important to confirm whether corrosion is on the outer surface or not.
General inspection capabilities
The Profiler enables inspections on material thicknesses up to 50mm total thickness (25mm single-wall thickness) for steel.
Using a low radiation source restricts the penetration capability of the energy but allows the operator to work without cordoning off any areas and can be deployed by rope access. For the Profiler, the absolute maximum thickness of steel the energy can penetrate is 50mm and by 33mm it is may be hard to identify shallow defects and confidence is reduced. The double wall thickness measured when inspecting pipe thicknesses using the system therefore results in a maximum pipe wall thickness of 19mm.
The Lixi Profiler measures loss of wall thickness and can detect changes from 1-3mm depending on material thickness. The technique can also detect the location of weld caps or blockages within the pipe Real time measurements meaning that it is relatively rapid.
The new version of the Lixi Profiler allows for inspection data to be “tagged” on the computer and a corresponding tag number may be inscribed on the pipe for matching defect location. Inspection data may be viewed on any spreadsheet program and even charted to view entire sessions at one time. The new Profiler incorporates software facilities to enhance the operator’s ability to identify potential areas of concern and make it easier to analyze results in real-time.
Operating Temperature
Non-contact so temperature not normally a limiting factor.
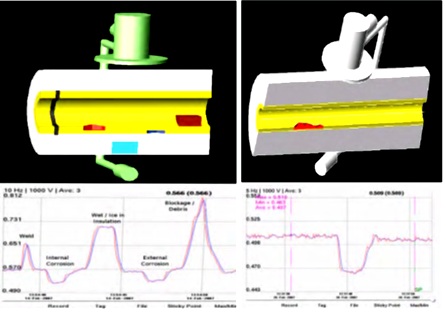
Samples of inspection information output in this method
Inspection limitations
Lixi Profiler C-scanner comes in three standard sizes: 6”, 13” and 18”.
Lixi Gadscope standard arm opening is 24”.
The absolute absorption of radiation by an object depends upon the thickness, density (porosity) and the atomic number of the elements present in the material No encoder is used to position the defects. This means that defect positions are not recorded by the system, but may be recorded by the operator on the insulation jacket at the time of inspection.
In common with conventional radiography, poor detection capability for narrow cracks and small isolated pits.
Access restrictions and component geometry limitations are restricted by the design of the equipment. Isotopes are governed by the Ionising Radiations regulations.
Access from opposite sides of the component is fundamental as the inspection data generated is based on the amount of radiation that has passed through the component
Unable to distinguish between inner or outer surface corrosion. Possible to discern between upper or lower wall thinning with an additional “slice” scan made perpendicular to the defect location.
Measurement may be affected when corrosion product is present. The lower density of loose corrosion product makes associated wall loss detectable although over-measurement is possible. Well-adhering corrosion product may
not be detectable.
Access requirements
Equipment needs to be in close proximity to the component. For Profiler using a low radiation source this can be done via rope access. Access to the component can be restricted by the C-arm as access is needed from two sides of a pipe to gain measurements.