Microwave
Microwave Technique
Microwave signals readily penetrate inside non-conducting materials and may therefore be employed for defect detection within these materials, but have no penetrating ability for conducting materials such as metals. Microwaves normally measure the dielectric properties of a non-conducting material.
Microwaves are radiated from the transducer to the specimen being tested. A detectable signal is returned at each interface where the dielectric constant changes (e.g. – where there are delaminations, cracks, holes, impurities or other defects). The transducer may be moved relative to the specimen at any desired speed and the scanning speed need not be uniform.
Once the data is collected, the software allows the image to be manipulated to enhance features. Also, since it is in digital form, the scan results can be stored and retrieved later to provide information on how a part or a defect has changed over time. This allows determination of the growth rate of a defect, which is critical to determining ultimate service life.
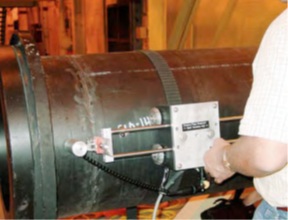
Equipments of method
General inspection capabilities
Detection of defects such as delaminations, disbands and impact damage in
dielectric materials such as fibre reinforced polymeric (FRP) materials.
Can operate in contact or non-contact mode, and from one side only or from both sides (reflection or through-transmission).
Full volumetric coverage can be obtained.
Inspection limitations
- Does not inspect sub surface defects in metal
- The microwaves do not penetrate fully through all pipe-repairs. Reasons for this might be further understood through trials but could be due to conductivity of carbon fibre in CFRP.
- Applicable to non-conductive materials only
- Moisture or liquid may affect results.