Quantitative Acoustic Emission Technique
All acoustic emission techniques (AE) aim for the detection and conversion of high frequency elastic waves emanating from a source to electrical signals. The elastic waves are generated when there is a re-distribution of stress in a material such as deformation or crack growth. The elastic waves are sound and ultrasound waves and are referred to as (AE) signals.
There are two major types of AE signals: burst (impulse) and continuous signals. Continuous AE signals are associated with processes related to plastic deformation development around flaws. The greater the volume of material involved in the process the higher the energy of AE signals.
Burst AE is associated with flaw elongation such as slip and dislocation movement, growth of cracks, twinning and phase transformations in metals. Once generated, the elastic waves will subsequently propagate to the surface where suitably mounted AE sensors will detect and record the waves. The resultant signals from the sensors are then amplified using a pre-amplifier before being analysed.
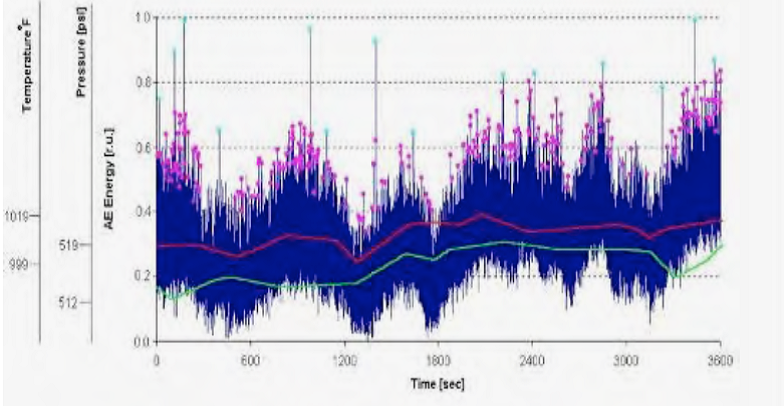
Conventional AE will only analyse the burst signals above the red line whilst QAE will analyse all signals (both continuous and burst signals)
Conventional AE only analyses the burst signals whilst QAE analyses both continuous and burst signals. This is a great drawback for conventional AE, for example in the case of silent cracks, the energy surrounding the crack absorbs the sound and will not be detected. This means that the QAE method is able to provide much more information about the component.
The QAE approach involves determination of the J-Integral value (the path integral around a crack tip representing the energy released per unit area). Information such as flaw location, crack kinetics and stress concentration can be detected.
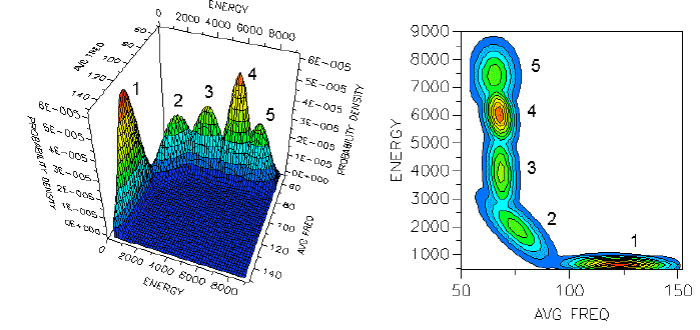
Ellipses of dispersion. 3D Normal distribution and Finger Prints calculated for the 5 stages of crack development. Stage 5 is the last stage before the crack becomes unstable.
It should be noted that QAE does not measure defect size, but detects stress displacement such as growth of defects or incorrectly loaded areas of pipework.
Detecting stress concentrations and over stressed zones can also be useful for assessing the condition of hangers and supports. A remnant life estimate and strategy for future inspection frequencies can also be decided from the output from QAE.
Hence, as with conventional AE, QAE provides a means to more targeted NDT.
There may also be commercial and health & safety savings in that there is a reduced requirement for scaffold and insulation removal/replacement.

QAE equipment attached to the component and after completed seal of insulation
General inspection capabilities
- Early detection of inner, outer and embedded flaws of the structure, including cracks and stress concentrations
- Inspection during plant operation, without shut down
- Ability to predict remnant life of the component
- The ability to detect and monitor stress corrosion cracking (SCC) and very early stages of creep.
- Full inspection coverage of component.
- Is also able to detect uneven stresses placed on the component such as problems with hanger and support designs.
Inspection limitations
Will only detect “active” defects (stagnant defects do not induce stress concentrations).
• Conventional NDT or metallurgical investigations are necessary to establish defect sizes.
• The method is not a continuous on-line monitoring method. After equipment is installed, the frequency of screening/monitoring of the component will be agreed with the client.