Thermography Technique
Thermography measures surface temperature. It can amongst others be used to measures water presence in insulation or damage of insulation through variations in surface temperature or to detect sand levels and build ups in pipe and vessels. Other applications include integrity of electrical components and as an aid in vibration analysis.
Thermography is a remote condition monitoring technique which identifies the surface temperatures by the measurement of the intensity of infra-red radiation emitted from a surface. Infrared energy is generated by the vibration and rotation of atoms and molecules. The higher the temperature of an object, the higher the emitted infrared energy due to more motion in the atoms and molecules. This is the energy detected by infrared cameras.
The cameras do not see temperatures but detect the thermal radiation emitted from the component.
The presence of water will be measured in terms of temperature variations (e.g. variations of emitted infra red radiation) of the insulation weather proofing along the pipe, arising from a loss in thermal efficiency of the insulation system.
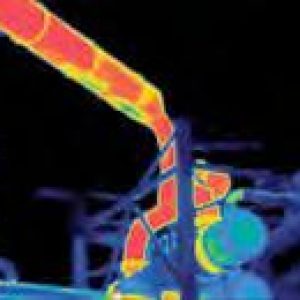
Flir ThermaCAM™ P65
General inspection capabilities
Resolution up to 0.1°C can be detected depending on camera and extra options utilised.
Thermal camera pixels (governs the smallest detectable “hot spot”) ranging
from: 320 x 240 for the expensive cameras to 16 x 16 for the budget options.
If a standard 20 degree IRISYS imager is used to look at scene 5 metres away, it will accurately be able to measure ‘hot spots’, which are larger than 11cm that cover a pixel.
A low resolution Flir camera will measure hotspots from 10mm at 5 metres (and hotspots from the size of 6mm for the higher resolution option).
Cameras with 0.02°C thermal sensitivity are used for dynamic images.
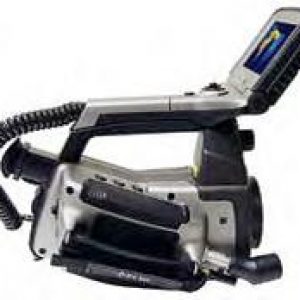
Inspection limitations
* Results can be distorted if hot pipes and shiny cladding are present close to inspection area – something that is likely to happen in reality. Preferable to carry out inspection after heavy rain to obtain “worst condition” data. A large enough temperature gradient required at the surface where the insulation is damaged for detection.
* For CUI inspections a 30°C temperature gradient across the insulation (between pipe and environment) is desired to ensure detection.
* The method is only detecting presence of water. On hot components the insulation might be drying rapidly and therefore only be wet for a very limited time. The defective/moist zone might then not be visible to the infrared camera.
Access requirements
Distance does not effect the measurement. However, infrared instruments measure the energy from a circular spot on the target, the farther away from the target the sensor is, the larger the spot. Consequently, distance is limited by the size of the object and the distance to the object you want to measure. Flir recommendations 10-12 meters. The camera could be mounted on carrier if needed.